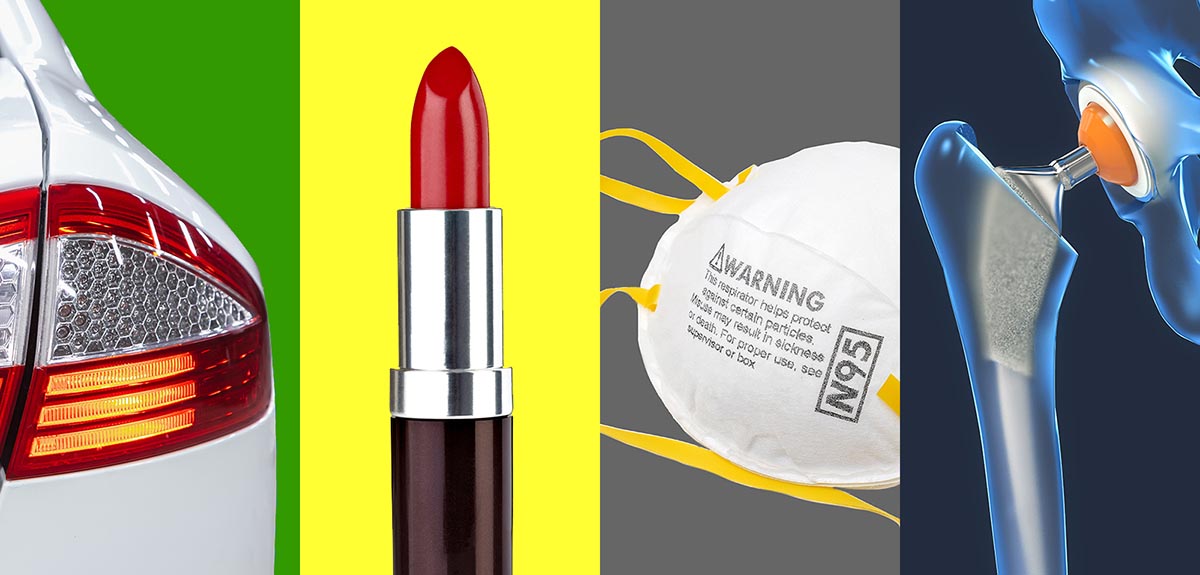
By Molly A. Seltzer
When people think about carbon, they rarely think of it as a building block of plastics and of common items in everyday life, from headphones to clothing to car parts. Paul Chirik, the Edwards S. Sanford Professor of Chemistry, recently discovered a new molecule and process for chemically recycling plastics, opening the door to sequestering carbon in the things we use and managing plastic waste on a large scale.

His research team, including first author of the study Megan Mohadjer Beromi, found that the common molecule, butadiene, which is produced in mass as a byproduct of fossil fuel development and also is an abundant organic compound, could be turned into a new polymer, oligocyclobutane, referred to as the “polymers of squares.” Polymers, long chain-like molecules, are the foundation of plastics. Oligocyclobutane has properties that can not only make a hard, strong plastic, but in a rare feature, can also be chemically broken down and returned back to butadiene. The process of both creating the polymer and recovering the building block, butadiene, relies on a unique iron catalyst, which the team discovered. It is the only known trigger that enables both the creation of this new plastic base and the reversibility of the process.
Here, Chirik comments on what challenges are left to refine the chemical process and how it could be scaled, along with his vision for a world in which carbon pollution is effectively managed.
What’s the central theme of your latest finding? Can you explain the concept of depolymerizing, or chemical recycling?
Paul Chirik (PC): We found that we can chemically recycle a material and recover its original building blocks. Imagine a world in which one could make a pipe, use the pipe for 20 years, recover the pipe, and break it down using a chemical process that recovers the butadiene, its primary building block. We’ve discovered a chemical process, an iron catalyst specifically, that enables a material that one day could be used for something like this. It allows us to effectively un-bake the cake and get back the ingredients. In theory, it could be 100% efficient, and it could be done over and over. It’s never been done before with a material as common and useful as this one, butadiene, which is the building block for polybutadiene, the rubbery material that makes up shoe soles, tires, and many other common items and is one of the principal building blocks used in the petrochemical industry.
How does this process play into the notions of a circular economy, waste reduction and decarbonization, or removing carbon from things or the atmosphere?
PC: With this process, what we’ve done is sequestered and further extended the life of hydrocarbon molecules. In the future, if and when this is commercialized, carbon will not be sequestered in a mine somewhere or underground in an aquifer as carbonate of CO2. It will be sequestered as building materials, such as the pipes in your house, a bridge, or your office. These materials won’t be taken to a landfill to decompose and release CO2. They would ideally be returned to the factory where they were made, and their carbon bases would be recovered and used to make new products.
Decarbonizing is a really tough word. I don’t think you can decarbonize completely. What we’re really talking about here is carbon management. Your lipstick, your hip implant, your IV bag, your N-95 mask are all made from byproducts of refining natural gas and refining petroleum, and they are all composed of carbon and hydrogen. But the carbon management process that we have enabled is to make the polymer, then make the plastic or product from it, use it, and when it is at the end of its useful life, add a catalyst and recover the original building block back. In theory, this could limit the amount of butadiene or fossil fuel byproducts that are needed in the first place, reducing the need for fossil fuel extraction.
Can you explain the chemical process in more detail and share what’s so special about this molecule and catalyst?
PC: I think what people may not appreciate is that there are effectively six molecules that build up most of the world’s plastic economy. You have six Legos: ethylene, propylene, xylene, benzene, toluene, and butadiene. To discover a new molecule made out of those six is unheard of, but it is what we have done. This is effectively a new way to snap Legos together. Usually, polybutadiene is made by hooking butadiene bits together with two double bonds. This produces linear molecules, big long chains of spaghetti that, when you cook them, get all intertwined. That’s why it’s rubbery. What we’ve done is learned to take a carbon-carbon double bond and make a square. People had thought of this before, but we have now discovered a metal catalyst that could actually achieve it, and that is the game changer.
People have demonstrated polymers can be chemically recycled before, but the problem is that they come from Legos that are not from fundamental building blocks, and are thus uncommon or impractical. Butadiene, by contrast, is used to make the rubber in tires, carpets, latexes, neoprene for gloves, wetsuits and foams. It is a widely applicable building block. If you start with a more esoteric Lego piece, researchers may be able to make the polymer in the lab and chemically recycle it, but it would not be used for a yogurt cup because it is more expensive than the yogurt itself.
Also, most polymers are usually too stable and require too much energy to chemically break them down. The key with our reaction is that the polymer, the chain of squares, are just about the same energy as the monomer, butadiene. You’re on a seesaw and you can go back and forth. That’s one of the big innovations here.
What are some of the challenges that remain with this technology?
PC: We have just scratched the surface in terms of exploring this polymer and catalyst further and potentially making truly recyclable things from them. The polymer we have made is barely a polymer, meaning it is not very long. We have studied some of its properties, such as how hard it is and its melting point, but we do not know the extent to which it could really be used. We also know that we can always make a catalyst that is faster and cheaper to manufacture. We need better catalysts. Right now, chemically recycling the polymer is slow and hard to do. It is there in principle. But it is sensitive and finnicky, and it needs engineering. Industry could make the polymer today, but could not depolymerize it yet. Even if researchers could make a yogurt cup from our new polymer, it’s not as if you take your cup, throw it in a beaker, and out comes the monomer again.
We need to further study the polymer and also the catalyst. On the fundamental chemistry side, why hasn’t this been discovered before? People have been polymerizing butadiene since 1920. What it means is that the iron catalyst we used is pretty special. There’s a lot of chemistry that must go into understanding why this one catalyst is giving us this one result. Does it have to be iron? Does it need the same structure we’ve put around the iron to work? We have all those questions to answer and that is the fun part.
What else is important to get this to work in practice and at scale?
PC: One would need to reprocess the polymer at a recycling plant or ideally at the place where the polymer was made. What we showed is the polymer is extremely stable. Without the catalyst, it can withstand temperatures up to 400 degrees Celsius or over 750 degrees Fahrenheit, without losing its stability. This shows its strength as a plastic. It is only when the catalyst is added that this new plastic depolymerizes or goes back to its monomer state, or to its original building block. And, it does not require extremely high temperatures to recycle, about 40 or 50 degrees Celsius with the iron catalyst.
Designing things for end of life is the key to moving toward a circular economy. But that is hard because usually the world works by rolling the ball down the hill. We take things with high energy and make them into things that have low energy. We do not live in a world where most of the products we use are energetically equal to the building blocks from which they came.
In addition, we need to develop a market for these products. I know that the chemistry we have done looks good, but if whatever is being made out of the butadiene does not appeal to customers, then it will not take off. SunChips once attempted to make a bag for better end-of-life recovery, and it turned out that the material made the bag crackle loudly as it opened, and people stopped buying them. This is what I mean when I say there are hurdles to clear beyond the chemistry. But the grand vision is to substantially reduce the amount of plastic waste, carbon emissions, and the use of fossil fuels. This process allows us to theoretically use without consuming, and that is what makes this work so important.