By Sharon Adarlo
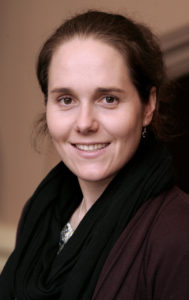
Concrete, considered the second most consumed material on our planet after water, is everywhere and has given shape and structure to buildings ranging from the mundane to the dramatic white shells of the Sydney Opera House.
However, the large volume of concrete produced does present environmental challenges. Portland cement, a fundamental constituent in concrete, emits nearly one ton of carbon dioxide for every ton produced and accounts for five to eight percent of global carbon-dioxide emissions.
Materials science researchers have been busy trying to formulate and study more sustainable alternatives to Portland cement that emit less carbon dioxide. Recently, a group of major oil and gas companies, the Oil and Gas Climate Initiative (OGCI), announced they would fund Solidia Technologies, a cement and concrete technology company claiming production methods that slash the carbon footprint of concrete by up to 70 percent and water consumption by 60 to 80 percent. OGCI, whose members include BP, Shell, Saudi Aramco, and seven other companies, controls a $1 billion investment fund earmarked for promising technologies and business models that can significantly reduce greenhouse gas emissions. The amount awarded to Solidia was not disclosed in news articles, nor were the details of the project.
To comment on this move and explain the science behind green cement, we turn to Claire White, assistant professor of civil and environmental engineering and the Andlinger Center for Energy and the Environment, for the latest, “Andlinger Center Speaks,” a Q/A series on timely energy and environmental topics with Princeton faculty and researchers.
White and her team of researchers are dedicated to finding alternatives to Portland cement for use in buildings, as well as for specialized high-temperature uses, such as in fire walls or in kilns and furnaces. White earned bachelor degrees in civil engineering and physics from the University of Melbourne, Australia in 2006. She earned her doctorate in chemical engineering from Melbourne in 2010. She joined the Andlinger Center in 2013 and is also an associated faculty member in the Department of Chemical and Biological Engineering, the Department of Mechanical and Aerospace Engineering, the Princeton Institute for the Science and Technology of Materials (PRISM), and the Princeton Institute for Computational Science and Engineering (PICSciE).
What is the significance of the OCGI funding?
The push from large companies to fund greener alternatives to Portland cement for construction and infrastructure will incentivize and promote the use of a range of new and innovative concretes. Hopefully this push will pave the way for all end users of concrete to see that greener alternatives are available and viable, leading to the development of extensive supply chains that enable these materials to be used where local resources are available. These alternative materials do exist, and certain types have been showcased in numerous large-scale case studies around the world, including in Australia and South Africa. Yet, construction standards (i.e., codes that do not allow alternatives) and lack of supply chains mean that penetration into the market has yet to occur. In some ways, this is a low-hanging fruit in a business sense. Alternative cement materials have the potential to revolutionize the construction industry.
Could you tell me about Solidia Technologies? How is their product different from Portland cement, and why is it considered green?
Solidia is based in Piscataway, New Jersey, and was founded by Richard Riman, Distinguished Professor of Materials Science and Engineering at Rutgers University. The concrete the company produces is different compared to Portland cement concrete. At the start of the production process, they make a specialized powder that subsequently reacts with carbon dioxide to form the mechanically hard material. This powder is mixed with sand prior to the addition of carbon dioxide. In Portland cement concrete, you use water to react with the cement powder to solidify the materials into concrete. In Solidia’s process, they actually flow carbon dioxide into mixture using water as a carrier. This causes the powder to react with carbon dioxide to harden the materials into concrete. Instead of emitting carbon dioxide in the process of producing concrete, this new cement actually uses carbon dioxide.
Solidia’s technology has many advantages. It’s a greener, more sustainable process because it sequesters carbon dioxide, a greenhouse gas. The chemistry demonstrates that you can produce strength-giving material with substantially lower carbon dioxide emissions. That’s a good thing.
Are there any drawbacks to their technology?
Some concrete is reinforced with steel. When you have concrete with steel, you want the internal pH in the concrete to be high (pH of 12 to 13) in order to prevent steel from corroding.
For the Solidia concrete, the carbon dioxide acts as an acidifying medium, so the internal pH is lower. This means they can’t use steel rebar for reinforcing concrete structures. But they may have other options to reinforce this concrete that doesn’t rely on having a high internal pH.
To get around that, Solidia usually manufactures precast blocks that don’t require rebar and can be stacked and assembled on site.
Let’s examine another green concrete, alkali-activated concrete, which is made up of cement derived from blast furnace slag (also known as alkali-activated slag), a glass-like material that is a byproduct of steel production, and coal-derived fly ash. This type of concrete has a high internal pH and can be used with the steel rebar used in present day concrete.
Can a structure in the future potentially be made up of different types of green concrete?
Yes. When it comes to the cement and concrete industry and the way forward in reducing greenhouse gas emissions, it won’t be one technology or one alternative concrete technology that is going to fix everything. When you are building a structure, manufacturers, engineers, and architects have to ask what is the purpose of the concrete, and what the local resources are at disposal. They will have to consider whether they need steel in concrete to withstand the tensile loads, and whether fibers, for example, can be used instead of steel rebar. For certain applications, Solidia’s cement alternative would be a fantastic option.
Why is studying greener alternatives to concrete and cement so exciting?
It’s such a complex material science area that until recently a lot of people shied away from it because it is really difficult to determine the intricate chemistries and physics that are responsible for the materials’ performance. It’s almost as if we take for granted that we have this construction material that works, and it works miraculously. That’s fantastic. But once we start changing the chemistry of concrete, such as for these green alternatives, we need to understand the fundamentals. It’s one thing to see at the macroscopic level new materials performing in a structural setting, but it’s another thing to be able to understand and predict the performance of a new cement, both for the immediate term and the future, based on the starting ingredients. This is where the fundamental materials research comes into play.
It’s a very complex puzzle. Being able to fit the puzzles together for a new concrete is very exciting.