Experts tackle industrial decarbonization at Andlinger Center retreat
Cutting carbon emissions from heavy industry will require sustained collaboration and innovation, experts agreed at the eleventh annual E-ffiliates Retreat hosted by the Andlinger Center for Energy and the Environment.
The event united leading voices from academia, companies, non-profits, and government around a shared goal of lowering the industrial sector’s carbon intensity. The sector, which includes industries such as cement and concrete production, iron and steelmaking, and chemicals manufacturing, accounts for almost a third of the carbon emissions generated each year in the United States.
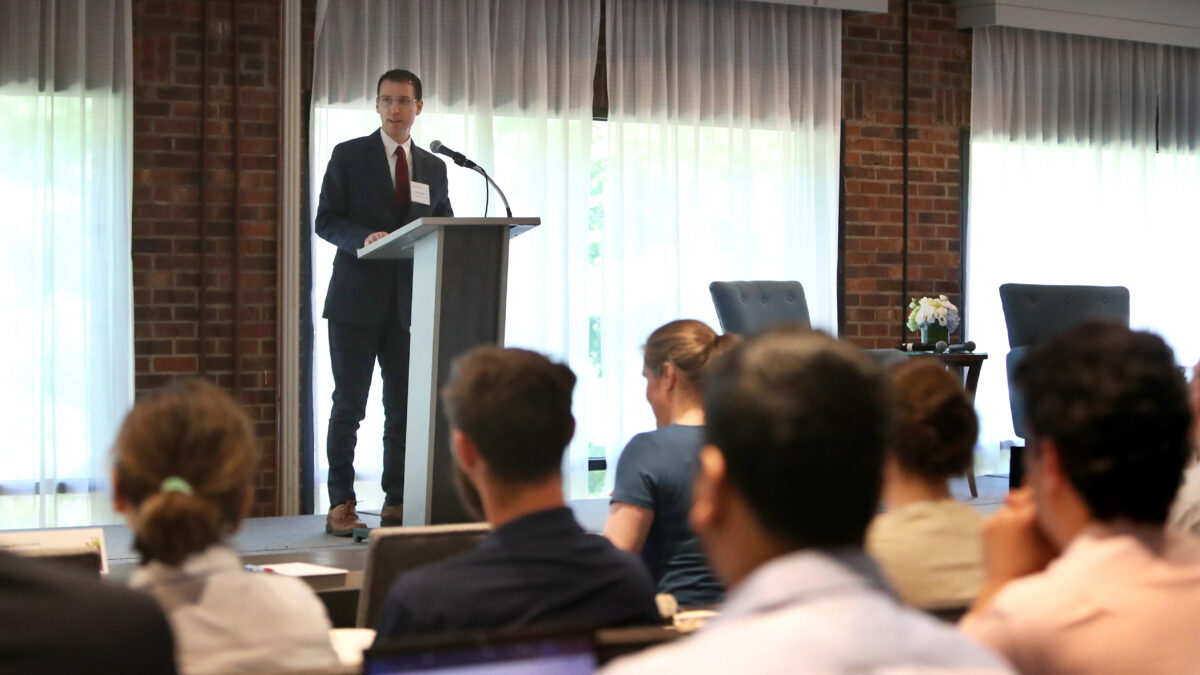
Yet in his keynote address, Paul Majsztrik, Program Manager for the Energy- and Emissions-Intensive Industries within the U.S. Department of Energy (DOE) Industrial Efficiency and Decarbonization Office (IEDO), said the wide range of manufacturing processes and complex supply chains inherent to the industrial sector make it among the most difficult to decarbonize, with no clear one-size-fits-all solution. For example, he highlighted a projection from the International Energy Agency that 60% of emissions reductions from heavy industry will come from technologies that are currently not market ready.
“Innovation in the industrial sector has been historically driven by factors like profit, competition, and energy cost. Only recently have we started to talk about carbon as a driver of innovation,” said Majsztrik. “I see this as relatively good news. We now see a tremendous interest in the idea of zero-carbon industry from researchers and industrial leaders alike. This is an extremely encouraging and exciting time for the industrial sector and a wonderful opportunity for impactful innovation.”
Even as Majsztrik acknowledged the difficulties of cutting industrial emissions, he said he sees industrial decarbonization as an opportunity for companies to transform their businesses in a way that provides a strategic advantage. He highlighted the work of his office to invest in innovative research projects seeking to develop and scale alternative materials and processes that could help to decarbonize these hard-to-abate industries. He noted that many of IEDO’s funded projects have strong potential to create new products and processes with high value, low emissions, and extremely high energy savings over existing industry benchmarks.
“As the saying goes, ‘the best time to plant a tree was 20 years ago. The second-best time is today,’” said Majsztrik. “Let’s work together now and do the R&D needed to develop all the innovative tools we need to fully decarbonize industry and meet our net-zero 2050 goals.”
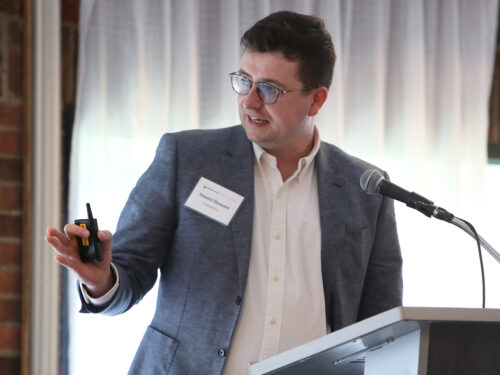
Majsztrik’s call for R&D was echoed by Daniel Stewart, a senior steel industry engineer at Energetics, during a panel on low-carbon iron and steelmaking. The panel explored some of the challenges associated with lowering the embodied emissions of iron and steelmaking both domestically and internationally while discussing how recent innovations could dramatically lower the carbon intensity of each process, such as integrating green hydrogen into existing iron- and steelmaking approaches.
“Most of these technologies are still nascent. They still have a lot of risks on the development side. But the upsides are potentially huge,” said Stewart. “The key is a sustained R&D campaign to push these technologies forward. We don’t need just one silver bullet — we need a whole case of them.”
Speakers on the panel also pointed out that the pathway to lowering emissions from iron and steelmaking will look different across the globe. In most of the world, iron and steelmaking commonly occurs in blast furnaces that depend upon coal as a key process input. Thus, continued efficiency improvements to blast furnaces or entirely different processes altogether will be critical for abating emissions in those countries — especially since many of those locations also coincide with rapidly growing human populations.
“Unlike with fossil fuels, which will eventually reach a peak usage level, there is no peak steel or materials in our future,” said Robert Kumpf, who is a Managing Director and leader in Deloitte’s Energy and Chemicals Practice. “We’re chasing decarbonization in a growing market.”
Like steel, concrete is another hard-to-decarbonize sector that won’t be going away any time soon.
While introducing a panel on low-carbon cement, Claire White, professor of civil and environmental engineering and the Andlinger Center for Energy and the Environment, said that in 2020 alone, the world used 30 gigatons of concrete — the equivalent of around 4,200 Hoover Dams.
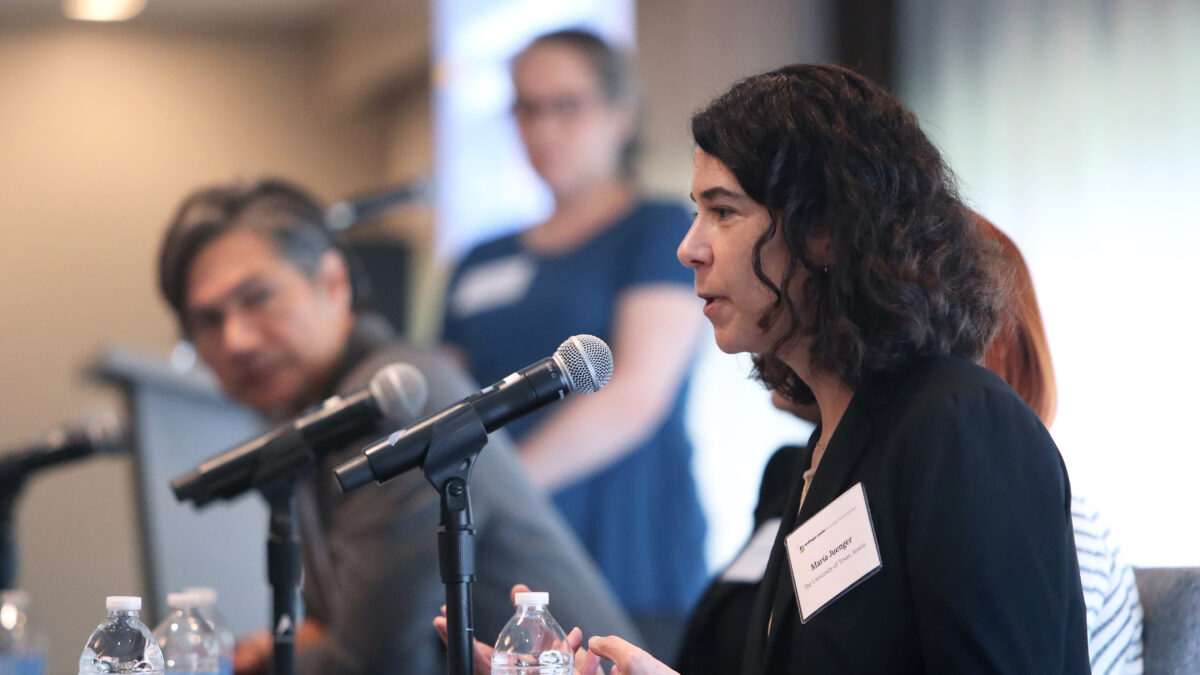
Concrete can be particularly hard to decarbonize because creating Portland cement — the primary binding agent for concrete — requires heating materials to temperatures as high as 1450 °C to ensure the proper composition, and because the primary component of Portland cement is limestone (CaCO3), which releases carbon dioxide as it decomposes during the heating process.
The challenges of abating emissions from cement production are reflected in the Global Cement and Concrete Association’s Roadmap to Net-Zero, which relies significantly on some form of carbon capture. However, panelist Davide Zampini, vice president of global research and development at CEMEX, emphasized that the current pathway to net-zero emissions in the cement and concrete industry is only a snapshot that reflects current technologies.
“What we have is a static picture of what’s available to us today,” said Zampini. “But I think heading into 2030, we’re going to see many new ideas and technologies coming from academia and companies that will provide a portfolio of innovation for us to move forward and alleviate the dependence on carbon capture and storage.”
In fact, panelist Maria Juenger, the L.B. (Preach) Meaders Professor of Engineering in the Maseeh Department of Civil, Architectural and Environmental Engineering at The University of Texas, Austin, pointed out that research interest into alternative, low-carbon cements is at an all-time high. Within the span of her career, Juenger said she has been encouraged to see cement materials research grow from an isolated interest into a vibrant research community, with many bright minds now working toward low-carbon solutions.
“It’s no longer just about solving structural engineering problems. We’re trying to solve sustainability challenges,” Juenger said.
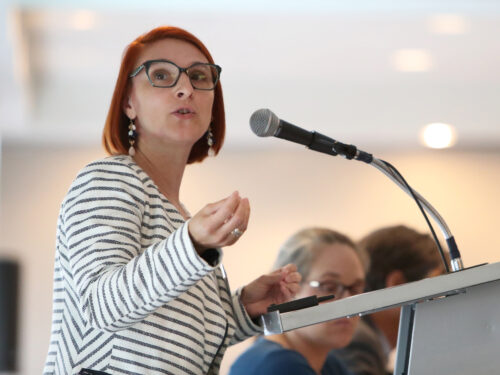
Even with growing interest in sustainable cements, Isabelle Rojas, senior principal scientist and program supervisor at Energetics, said that the structural stability and perceived newness of alternative building materials remain concerns for end users. Often, she said, building codes and standards favor the status quo of tried-and-true building materials. Furthermore, many in the industry may be hesitant to switch from familiar products to low-carbon cements, which may require different input materials or production processes.
Yet Rojas also pointed to commitments from big buyers such as the U.S. government’s Buy Clean initiative, which prioritizes the purchase of low-carbon building materials for federally funded projects, that could be a key lever to kickstart markets and increase acceptance of sustainable building materials.
“Moving forward into the next stages of industrial decarbonization, we should be thinking creatively about how the government can help to take on some of the perceived risks associated with these sustainable alternatives,” Rojas said.
Expanding on Rojas’ point, much of the discussion in the day’s final panel centered on the role of the public sector in de-risking new technologies. While some panelists expressed some concern that the U.S.’s incentives-driven model might be insufficient to achieve a fully decarbonized industrial sector, Harry Warren, president of CleanGrid Advisors LLC and a non-resident fellow at the Andlinger Center for Energy and the Environment, said he was hopeful about the magnitude of the U.S.’s investment in new technologies and the potential for that investment to accelerate decarbonization efforts across the globe.
“Most of the big companies in these heavy industries have a very global footprint,” Warren said. “What we may be seeing is that companies are looking to initially demonstrate technologies in the U.S. that will end up having worldwide applicability for them.”
White’s closing remarks acknowledged the challenges of making rapid changes to lower the carbon intensity of the industrial sector. But she also said she has been encouraged to see that stakeholders from across the industrial sector are starting to have serious conversations about reducing emissions and is hopeful that the momentum for sustainable solutions in the sector will only continue to grow.
“We’ve seen today that industrial decarbonization is an incredibly complex problem that requires extensive collaboration, from materials researchers all the way to the end users. And I think it’s clear that we are standing at the beginning of the challenge, not the end,” White said. “But I hope that the conversations we’ve begun today are also the start of some meaningful collaborations to push forward on the road to net-zero industry.”
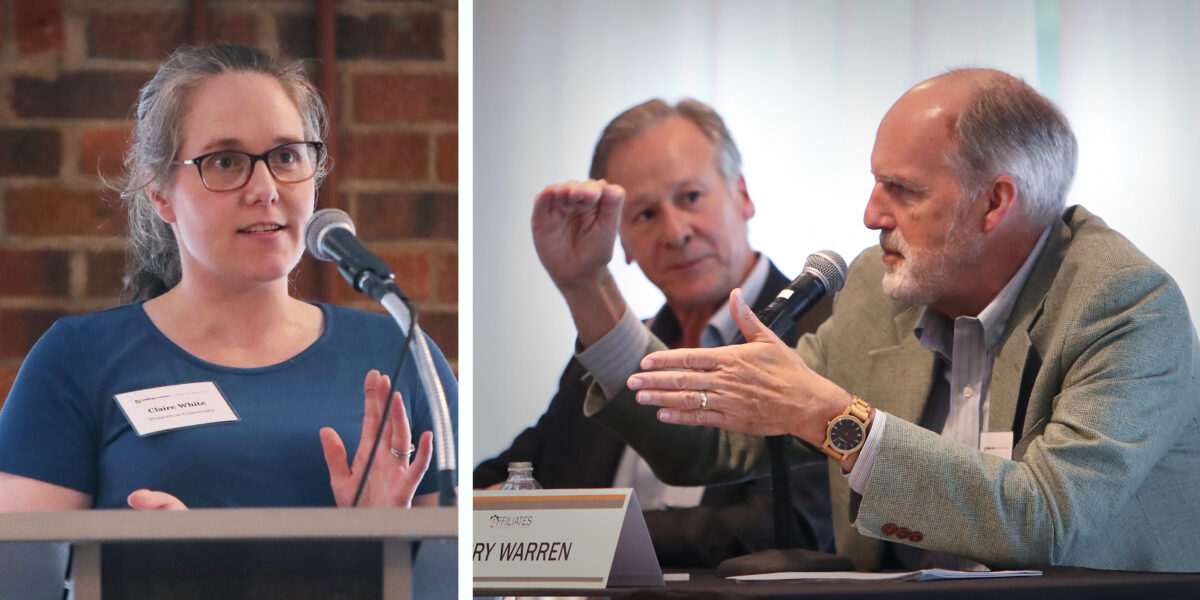